株式会社 テクニスコ【代表取締役 関家 圭三】(以下「テクニスコ」という)は、国立研究開発法人 産業技術総合研究所【理事長 中鉢 良治】(以下「産総研」という)集積マイクロシステム研究センター【研究センター長 廣島 洋】化学バイオインターフェース研究チーム 井上 朋也 研究チーム長と共同で12 cm x 18 cmのサイズのフローリアクターを開発した。
今回、テクニスコのクロスエッジ®微細加工技術を駆使した8インチMEMSプロセスを用いて、産総研のシーズ技術であるマイクロリアクターを12 cm x 18 cmまで大型化した。リアクターあたりの製造量は10倍以上向上している。反応リスク管理の観点から、医薬品やファインケミカル製造用のフローリアクターへの応用が強く期待される。
なお、この技術の詳細は、平成27年8月27日~28日に東京ビックサイトで開催されるJSTフェア2015で発表される。
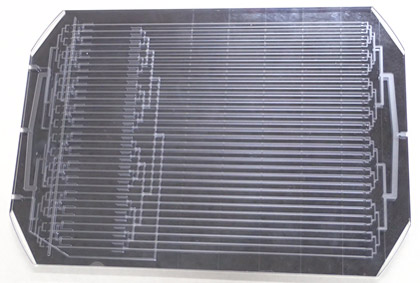 |
開発したフローリアクター |
最近、医薬品やファインケミカルの製造技術として、従来のバッチプロセスに代わるフロー反応システムが注目を集めている。特に近年、世界的大手製薬企業がフロー反応システム技術の採用を発表するなど、利用拡大が見込まれている。
しかし、システムで用いられるリアクター(反応器)は、加工技術上の制約から構造が限定されるため適用できる反応に限界があり、特に固体触媒を用いる反応には不向きであった。
産総研は、微細加工技術により熱・物質移動効率を高めたフローリアクターである独自のマイクロリアクターの開発を進めていた。特に水素と酸素の直接反応による過酸化水素の製造に関して、従来の条件より低圧、常温で実用濃度である10 %の過酸化水素を高効率で製造できるリアクターを開発してきた。マイクロリアクター技術により水素や酸素の爆発リスクを回避できたこと、最適な反応場を実現して反応条件を温和にできたことがかぎであった(2010年9月14日産総研・三菱ガス化学共同プレス発表)。
当初の10 %過酸化水素の製造能力が40 g/日であったため、テクニスコとの共同研究によりフローリアクターの大型化と並列運転による製造能力向上をめざした。
なお、本研究開発は、国立研究開発法人 科学技術振興機構の委託事業「研究成果最適展開支援プログラム(A-STEP)ハイリスク挑戦タイプ(平成25~26年度)」による支援を受けて行ったもので、産総研の実用化への橋渡し活動の一環である。
今回、産総研のもつシーズ技術であるマイクロリアクター技術に対して、テクニスコのクロスエッジ®微細加工技術を駆使してB6サイズ(12 cm x 18 cm)のフローリアクターを精度良く製造した。このフローリアクターは3層のガラス基板から構成されている。図1はフローリアクターの整流機構部分であり、50 μm幅のチャンネルとサブミリメートル幅のチャンネルを精度良く3次元的に構築してある。B6サイズのフローリアクター製造プロセスは8インチのガラス基板やシリコン基板を丸ごと用いる8インチプロセスとなる。一工程での瑕疵が歩留まり0に直結するため、各工程をミス無く行うことが重要である。テクニスコのクロスエッジ®微細加工技術により、マイクロチャンネル内の傷(チッピングなど)がなく、寸法精度が向上、さらに溝加工を施した基板間の密着性が向上して、世界的にも例のない8インチMEMSプロセスによるフローリアクター製造を実現できた。なお、テクニスコではフローリアクターをはじめとしたマイクロ流体デバイスを8インチ基板対応のMEMSプロセスにより製造できる環境を構築している。
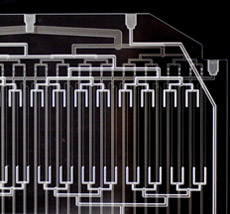 |
図1 B6サイズフローリアクターの整流機構 |
過酸化水素製造では発熱量は約190 kJ/molであるが、フローリアクターが大型になると反応に伴う熱が蓄積して高温になり、製造された過酸化水素がさらに反応して水に転換してしまう問題が生じる。テクニスコでは今回開発したガラス製のフローリアクターに熱伝導度のよいシリコン基板を接合して、除熱効率に優れたフローリアクターを開発した。これにより空冷だけでも十分な除熱が可能となった。たとえばガラス製フローリアクター(図2左)を用いた場合には、リアクター温度が80 ℃付近まで急激に上昇するような反応条件であっても、除熱を強化したフローリアクター(図2右)ではリアクター温度が50 ℃以下に留まり、安定した反応が可能となった。また、過酸化水素の収率も向上した。
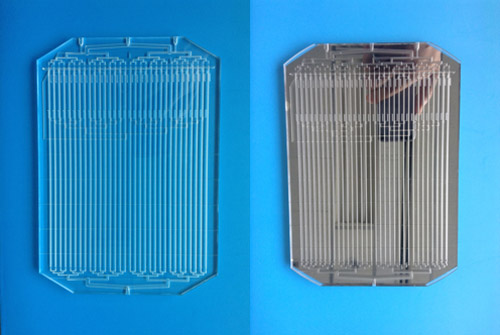 |
図2 ガラス製B6サイズフローリアクター(左)とシリコンにより除熱を強化したフローリアクター(右) |
さらに、反応器の4並列運転により10 %過酸化水素を2 kg/日の規模で製造できることを実証できた。並列運転において各リアクターに反応流体(過酸化水素の直接製造であれば水素、酸素、および水)がそれぞれ均等に供給されることが必須であるが、テクニスコのクロスエッジ®微細加工技術により加工性が向上したことで構造を簡素化できたため、より円滑な並列運転が可能となった(図3)。
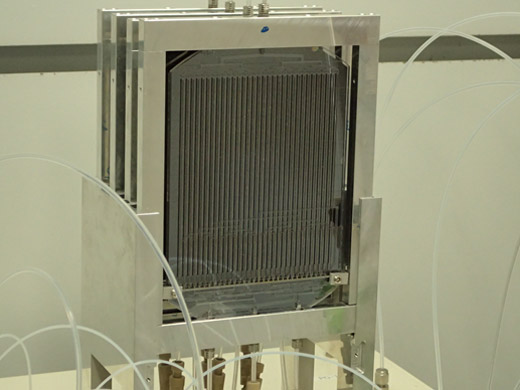 |
図3 シリコンにより除熱を強化したリアクターの4並列運転 |
医薬品やファインケミカルの製造では、温度を精密にコントロールする必要のある反応は少なくない。今後は、そのような反応にカスタマイズしたフローリアクターを受注生産する仕組みを整え、医薬品やファインケミカル製造におけるフロー反応プロセスの利用拡大に貢献していきたい。
また今回整備したマイクロ流体デバイス製造環境は、創薬支援などの用途のマイクロ流体デバイスを安価に供給する上でも有用である。そのようなデバイス開発・製造を通じて健康長寿社会実現に貢献していく。