独立行政法人 産業技術総合研究所【理事長 中鉢 良治】(以下「産総研」という)サステナブルマテリアル研究部門【研究部門長 中村 守】斎藤 尚文 上級主任研究員、金属系構造材料設計研究グループ 岩崎 源 客員研究員、千野 靖正 研究グループ長は、宮本工業株式会社【代表取締役社長 宮本 尚明】(以下「宮本工業」という)と共同で、マグネシウム合金の低温鍛造技術を開発した。
今回開発した技術は、あらかじめ鍛造素材の微細組織を結晶粒径10 µm以下に制御し、サーボプレスを用いて低速(5~10 mm/s)で鍛造することにより、通常、汎用メカニカルプレスを用いて400 ℃程度で行っているマグネシウム合金の鍛造温度を200 ℃以上低くすることを可能にしたものである。鍛造温度を低くすることにより、固体潤滑剤に比べて鍛造後の除去が容易である水溶性潤滑剤の使用が可能となるので、マグネシウム合金の鍛造部材の低コスト化や生産性向上が期待される。
なお、本鍛造方法の基盤となる研究結果は、2013年6月7~9日に愛知県名古屋市で開催される平成25年度塑性加工春季講演会で発表される。
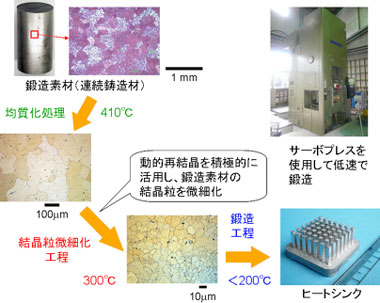 |
今回開発したマグネシウム合金の鍛造工程 |
マグネシウム合金は、構造用の金属材料の中で最も軽量であり、リサイクル性もあることから、輸送機器をはじめとするさまざまな産業への応用が期待されている。しかし、現状ではアルミニウム合金に比べるとその普及は進んでいない。これは、マグネシウム合金に固有の発火性、耐食性や塑性加工性の不足などの問題もあるが、最大の原因は材料コスト、加工・製造コストが高いことである。一般的にマグネシウム合金の鍛造は、鋳造-押出し-鍛造というプロセスを経るため、各工程でのコストが積み上がって高コストとなる。
これまで実用化されたマグネシウム合金部材は、ほとんどが鋳造法によって成形されているが、寸法精度、部材強度、生産性、生産環境などの点で難点があり、これらの点で優れている塑性加工技術の開発に大きな期待が寄せられている。塑性加工技術の中でも、鍛造技術については、高品質の部材が高い生産性で製造できることから、その技術の確立が産業界から求められている。しかしマグネシウム合金は塑性加工が大変難しい、高温鍛造に適さないなどの既成概念が根強いこともあって開発研究が遅れ、成功事例の報告も少なかった。
産総研は、平成18~22年に独立行政法人 新エネルギー・産業技術総合開発機構(NEDO)の「マグネシウム鍛造部材技術開発プロジェクト」において一般財団法人 素形材センターと共同で、マグネシウム合金連続鋳造材の新たな鍛造技術の開発を行ってきた。その結果、鍛造加工中に起こる動的再結晶という微細組織の変化を積極的に利用することにより鍛造素材の結晶粒を10 µm以下に微細化することができ、その結果、300 ℃で断面減少率81 %の前後方管押出し鍛造が可能になることを確認した。この新規鍛造技術は、素材の結晶粒を微細化する工程と、それに引き続いて形状を造る成形工程を一連の1工程として扱う点に特徴がある。
今回はこのプロセスを実製品に適用し、温度200 ℃以下での鍛造を可能にすることを目的とし宮本工業と共同研究開発を行った。
「マグネシウム鍛造部材技術開発プロジェクト」ではひとつの金型を使用して1工程で試作鍛造したため、成形工程の温度だけを低くすることができなかった。そこで今回は、結晶粒の微細化工程と成形工程を分けた2段階で鍛造を行った。いずれの工程も、鍛造にはサーボプレスを使用した。サーボプレスは加工速度やスライド位置の制御に優れるため、材料組成、加工温度、ひずみ速度に影響を受けるマグネシウム合金の動的再結晶による結晶粒微細化を制御するためには有用なプレスである。
今回、鍛造に使用したマグネシウム合金は、市販のAZ31(Mg-3 %Al-1 %Zn)マグネシウム合金連続鋳造材(直径155 mm)とAZ61(Mg-6 %Al-1 %Zn)マグネシウム合金連続鋳造材(直径55 mm)の2種類である。いずれも410 ℃で24時間の均質化処理を施されている。これらの素材を所定の直径と高さに加工して鍛造用ブランク材とした。試作鍛造品としては、角ピンヒートシンクを選択した。角ピンヒートシンクの基本構造は30 mm角×厚さ3.5 mm、角ピン部は2 mm角×高さ8 mmで本数は49本である。
微細組織を制御するための結晶粒微細化工程では、平均結晶粒径が100 µm以上のブランク材を、温度300 ℃で所定の圧下率まで据え込んだ。動的再結晶の進行とブランク材の工程初期の割れを防止する観点から、据え込みは平均速度5~10 mm/sの比較的低速で行った。図1に据え込み圧縮後のブランク材の微細組織を示す。AZ31マグネシウム合金連続鍛造材では一部に結晶粒径が10~20 µm程度の領域があるものの、それ以外では動的再結晶によって結晶粒径5 µm以下まで微細化している。一方、AZ61マグネシウム合金連続鍛造材でも動的再結晶が生じているものの、平均結晶粒径は10 µm程度とAZ31マグネシウム合金連続鍛造材に比べて少し大きかった。
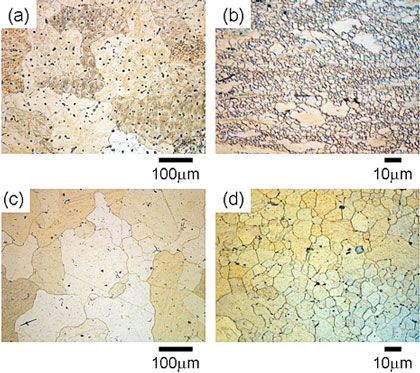 |
図1 マグネネシウム合金連続鋳造材のミクロ組織
(a) AZ31マグネシウム合金の結晶粒微細化処理前
(b) AZ31マグネシウム合金の結晶粒微細化処理後
(c) AZ61マグネシウム合金の結晶粒微細化処理前
(d) AZ61マグネシウム合金の結晶粒微細化処理後 |
図2に結晶粒微細化処理を施したAZ31マグネシウム合金の連続鋳造材を素材として今回開発した鍛造方法によって作製したヒートシンクの外観写真を示す。鍛造は、結晶粒微細化処理後の材料をブランク材とし、鍛造温度100 ℃、150 ℃、200 ℃で行った。平均の押出し比は4.6、平均押出しひずみは1.5、断面減少率は0.78である。材料の割れを防止するため、平均速度5~10 mm/sの比較的低速で鍛造を行った。いずれの鍛造温度でも割れはなく、49本のピンの高さが揃った健全なヒートシンクが鍛造加工できた。またAZ61マグネシウム合金の連続鋳造材を素材としても、今回の鍛造方法により同様のヒートシンクを作成できた。
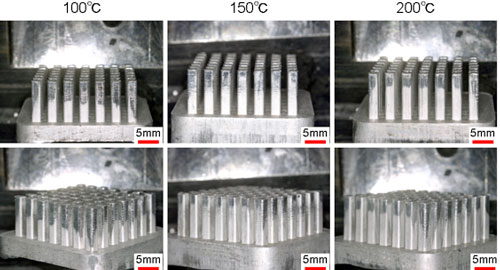 |
図2 AZ31マグネシウム合金の連続鋳造材から鍛造で製作したヒートシンクの外観 |
今回開発した低温鍛造方法により、高精度、低コスト、高生産性のマグネシウム合金鍛造部材の作製が期待される。また、鍛造温度が200 ℃以下であるため、水溶性潤滑剤も使用できるようになる。水溶性潤滑剤は、グラファイト系などの固体潤滑剤に比べて鍛造後の除去が容易であるため、マグネシウム合金鍛造部材の一層の低コスト化、生産性向上も期待される。
産総研と宮本工業は共同で、カルシウムを添加した難燃性マグネシウム合金やその他のマグネシウム合金に対しても鍛造温度低温化の可能性を検証する。