独立行政法人 産業技術総合研究所【理事長 野間口 有】(以下「産総研」という)先進製造プロセス研究部門【研究部門長 村山 宣光】セラミック機構部材プロセス研究グループ【研究グループ長 北 英紀】日向 秀樹 研究員らは、三井金属鉱業株式会社【代表取締役社長 仙田 貞雄】(以下「三井金属」という)と共同で、従来品に比べて耐熱衝撃性と高温での強度を飛躍的に高めた窒化ケイ素系セラミックスを開発した。
今回、窒化ケイ素(Si3N4)をベースとして、高い熱伝導率をもつ粒界相を形成させるとともに、そこに非晶質に近い窒化ホウ素(BN)のナノメートルオーダーの微粒子を分散させることで、耐熱衝撃性を飛躍的に向上させた。従来の窒化ケイ素が1000 ℃の温度差で強度が低下するのに対して、今回の開発材は、電気炉で1400 ℃に加熱した後水中に投下することを10回繰り返してもほとんど強度が劣化しなかった。また、この開発材について大気中1200 ℃で高温曲げ試験を行ったところ、室温と同程度の強度を保持していた。
セラミックスでは大型化すると小試験片では得られた特性が得られず、実用化を進める上での課題になることが多いが、この開発材では、焼結条件を最適化することによって、直径82 mm長さ370 mmの比較的大型の部品でも、試験片と同様の組織、物性が得られた。また、実際の製品形状に近い部品の焼成も可能となった。
この成果の一部は、独立行政法人 新エネルギー・産業技術総合開発機構プロジェクト「革新的省エネセラミックス製造技術開発」の中で応用されている。また、この成果は、平成22年11月14~18日に大阪市で開催される第3回国際セラミックス会議(3rd International Congress on Ceramics:ICC3)で発表される。
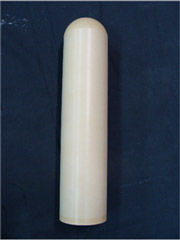 |
図1 試作した金属溶湯用管状部材(直径82 mm 長さ370 mm)
|
世界的に炭酸ガスの排出規制の動きがあり、鉄鋼分野や非鉄金属分野における製造プロセスの熱エネルギーロスの低減や鋳造部材の保守間隔の長期化が必要とされている。特に、アルミニウムなどの鋳造プロセスでは、これらの課題を解決するために耐熱性・耐食性に優れる窒化ケイ素セラミックスが保護管、ラドル、ストーク、ヒーターチューブなどの製造用部品として活用されている。しかし、窒化ケイ素自体は優れた高温特性や熱衝撃特性をもつ材料であるが、アルミニウム鍛造プロセスに比べて、より高温で、激しい熱衝撃に晒される鉄系材料の鋳造などに使用するには、その耐熱性・耐熱衝撃性が不足している。そのため、より優れた熱特性を示し、大型品や複雑形状品が製造できる窒化ケイ素系セラミックスの実現が望まれていた。
従来、耐熱衝撃性の向上には、(1)熱膨張係数を低減させる、(2)弾性率を小さくする、(3)熱伝導率を向上させる、といった手法が知られ、これまでは個々の手法を用いることで耐熱衝撃性を向上させてきた。しかしながら、これらの手法を個々に用いるだけでは、耐熱衝撃性が1200 ℃を超える材料は得られていなかった。また、第二相を添加して弾性率を低下させる手法では緻密化が進まず、ホットプレスなどの加圧焼結でないと材料が得られず、大型の部品や複雑形状の部品は作製できない問題があった。
産総研は三井金属と共同で、従来の窒化ケイ素セラミックスの耐熱衝撃性と耐熱性のさらなる向上を目指した研究開発を進めてきた。今回、室温強度の低下を抑え、熱伝導率の向上と弾性率低減を同時に実現するため、窒化ケイ素セラミックスを構成する粒界相の耐熱・高熱伝導化と第二相添加による弾性率低減効果を組み合わせる手法を試み、優れた耐熱性と耐熱衝撃特性を有する材料の開発を目指した。
まず、窒化ケイ素セラミックス粒界相の熱伝導率に着目した。粒界相は通常非晶質であり、熱伝導率を低下させる要因の一つとなっていた。そこで、粒界相の主成分を構成する焼結助剤として、結晶化すると耐熱性の高い粒界相を形成する酸化イッテルビウム(Yb2O3)を用いた。さらに、その量および焼成方法を制御し、焼結時に粒界相を結晶化させることで熱伝導率を向上させた。さらに、第二相として添加する窒化ホウ素微粒子の量を制御して、弾性率を低減するとともに、熱衝撃時に生じる応力を窒化ホウ素粒子部で緩和し、生じた微細亀裂がその後の熱衝撃においても進展しないようにした(図2)。
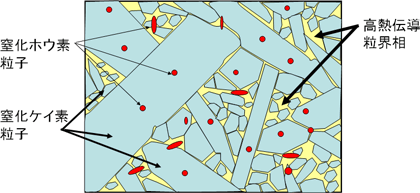 |
図2 開発した材料の微構造のイメージ図
|
この方法によって作製した窒化ケイ素系セラミックスは、1400 ℃の熱衝撃に対しても、強度劣化がなく、従来にない耐熱衝撃性を示した。また、繰り返し熱衝撃試験を行ったが、初期の強度を維持していた(図3)。
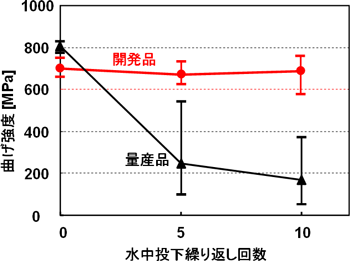 |
図3 1400 ℃での衝撃熱衝撃試験後の強度
|
このような熱的性質を実現するには結晶化した粒界相が、Yb4Si2N2O7という特定の結晶相であること(図4)、添加した窒化ホウ素粒子が、微細な状態で粒内および粒界に存在し、それが破壊の起点とならないように適正な分散状態で存在することが必要であることがわかった(図5)。また、その添加した窒化ホウ素粒子の量が適正であれば、従来の耐熱衝撃材料のように室温強度が大幅に低下しないで、高い室温強度と優れた耐熱衝撃性を合わせもつ材料が得られた。この開発材について大気中1200 ℃で高温曲げ試験を行ったところ、高温で軟化しにくい結晶性のYb4Si2N2O7粒界相が形成されているため、室温と同程度の強度を保持していた。一方で、この材料の焼結は非常に厳密に条件を制御する必要があり、これまでは試験片サイズ程度でしか作製できなかったが、今回、焼結条件の最適化によって、金属の溶湯部材で用いられる保護管、ラドル、ストーク、ヒーターチューブといった比較的大型の部品についても、試験片と同等の性能をもつ焼結が可能となり、実際の部品へ適用する可能性が大きく高まった。
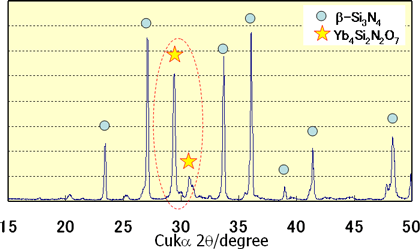 |
図4 開発した材料のX線回折パターン
|
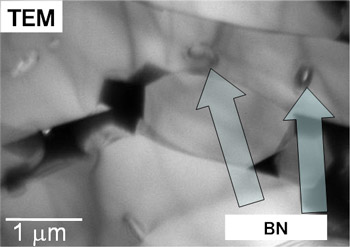 |
図5 得られた焼結体の透過型電子顕微鏡(TEM)による観察結果
|
今後は、今回開発した材料を使って、アルミニウム鋳造用だけでなく、亜鉛、鋳鉄、鉄鋼系の鋳造など、より過酷な使用条件のプロセスにも適用できる大型部品をターゲットとして部材化技術を確立し、実用化を図る。