独立行政法人 産業技術総合研究所【理事長 野間口 有】(以下「産総研」という)先進製造プロセス研究部門【研究部門長 村山 宣光】明渡 純 上席研究員 兼 集積加工研究グループ長と同グループ ダニエル ポポビッチ 産総研特別研究員は、トヨタ自動車株式会社【取締役社長 豊田 章男】(以下「トヨタ自動車」という)電池生技開発部【理事 兼 部長 石黒 恭生】藤嶋 正剛 グループ長、永井 秀幸 技術員らと共同で、産総研が開発したセラミックス材料の常温高速コーティングプロセスであるエアロゾルデポジション(AD)法を用いて、酸化物系の正極材料、負極材料、固体電解質材料を薄膜・積層化して、金属基板上に3層構造からなる全固体薄膜リチウム(Li)イオン電池を試作(図1)、蓄電池としての充放電特性を世界で初めて確認した。
従来型の薄膜技術とは異なり、AD法を用いると基板の加熱が不要で、また、厚膜化も容易である。そのため、成膜時間が大幅に短縮でき、蓄電池の生産性向上やプロセスコストの大幅な低減が期待される。今後はAD法を用いた本格的な全固体電池の共同開発を進めていく。
なお、本研究成果の詳細は、平成22年11月14日~18日に大阪市の大阪国際会議場で開催される第3回国際セラミックス会議(ICC3)で発表される。
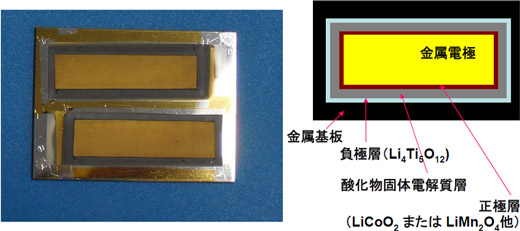 |
図1 今回試作した全固体型Liイオン電池
|
エネルギー・環境問題への取り組みとして、プラグインハイブリッド車や電気自動車の高性能化が、世界中で活発に行われている。このような中、大幅な性能向上には高エネルギー密度の次世代蓄電池技術の開発が大きな鍵を握っており、材料と製造方法の両面からの取り組みが重要になっている。
次世代蓄電池の1つである全固体型Liイオン電池は、不燃性で流動性のない固体電解質を用いるため、1つのケース中に複数の単電池を直列接続で入れるなど制御システムを簡素化でき、高エネルギー密度の電池パックが実現できると期待されている(図2)。
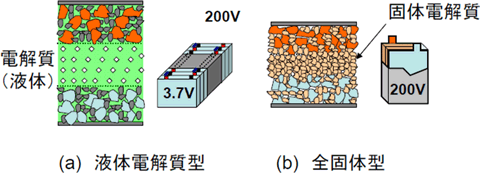 |
図2 従来の液体電解質型のLiイオン電池(a)と全固体型Liイオン電池(b)
|
産総研は、これまでに常温・高速のコーティング技術であるエアロゾルデポジション(AD)法によって、60 cm四方の高透明なセラミックス厚膜の常温形成に成功している(2004年5月20日産総研プレスリリース)。常温プロセスという特徴を活かし、平成18年度より、Li電池材料の薄膜化、厚膜化に取り組んできた。
一方、トヨタ自動車では、「石油代替エネルギーへの対応」、「CO2排出量の削減(地球温暖化対策)」、「大気汚染の防止」など低炭素社会に向けた活動を強化するために、ハイブリッド車技術を中心とした石油消費の抑制とエネルギー多様化への対応などに取り組んできた。その中で、代替燃料車であるプラグインハイブリッド車や電気自動車などの重要な鍵を握る電池に関して、現状の液系Liイオン電池の性能を超える革新的な次世代電池の研究開発を行っている。
産総研とトヨタ自動車は、両者の技術を融合させて次世代電池を開発するために、共同研究を開始した。
全固体型のLiイオン電池は、従来のLiイオン電池の液体電解質を固体電解質に置き換えたものであるが、電解質が固体であるため、イオン伝導度は液体電解質に比べてかなり低い。そのため、全固体型電池の開発では、電解質層でのイオンの移動性を高めるため、電気的な絶縁性を保ちつつ電解質層をいかに薄くするか、また、いかに高いイオン伝導度の固体電解質材料を発見するかが重要になっている。
これまでに、伝導度の高い硫化物系固体電解質を用いたバルク型電池の試作例が報告されているが、硫化物系材料は緻密な構造体作製や薄膜化が困難であるほか、水との反応で劣化しやすいことや硫化水素ガスの発生などの問題があった。また、常温で電解質材料を正極材料と負極材料で挟み込み、プレスして電池としているが、プレスによる成形では電解質層の密度が上がらないために特性が十分に発揮できないといった課題も抱えている。さらに、イオンの伝導が乱されないように、正極や負極と電解質層との間に綺麗な界面構造を作る必要があるが、これらの界面形成にも課題がある。従来の窯業的手法である焼結などで、正極材料、電解質材料、負極材料を積層化する方法があるが、電解質層を十分薄くするには、高密度の固体電解質層を形成する必要があり、高温での焼結が必要である。しかし、Li化合物は反応性が高く、各層の界面で相互拡散が起こり綺麗な界面を形成することが困難であった。スパッター法などの従来型の薄膜技術を用いた酸化物系の全固体薄膜電池の報告例もあるが、基板の加熱が必要で、成膜速度が遅く、大型化や低コスト化に大きな問題があった。
これに対しAD法では、原理的に高密度な固体電解質薄膜を常温で形成でき、正極層、負極層と積層化できる。今回、固体電解質としてLi酸化物系の各種材料を検討し、成膜条件や原料粒子をAD法に適合するように調整してイオン伝導度で3~5×10-6ジーメンス毎センチメートル(S/cm)の固体電解質膜を形成した。さらに、正極材料に LiCoO2やLiMn2O4、負極材料に Li4Ti5O12など良く使われる電極材料を用い、AD法により3積層化した(図3)。
AD法では、原料粒子が基板に衝突する際に3 ギガパスカル(GPa)以上の非常に高い圧力がかかる。従って、非常に高いプレス圧で原料粉末を粉体成形しているともいえ、常温プロセスで形成されたにもかかわらず、各層とも非常に緻密な膜構造を形成できた。また、基材や積層する下地膜表面のごく限られた領域にだけ高圧がかかるため、基板や各層界面へのダメージは小さく、熱による相互拡散も見られない。今回、正極、負極、電解質各層の膜厚を最適化し、酸化物系の全固体型薄膜Liイオン電池を作製し(図4)、さらに、世界で初めて充放電特性を確認した。
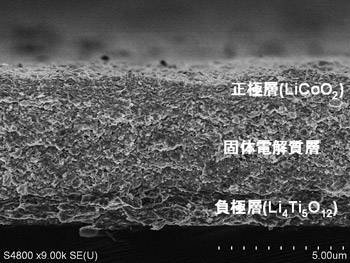 |
図3 正極層( LiCoO2または LiMn2O4)、負極層(Li4Ti5O12)で酸化物系固体電解質層を挟んで3積層化した膜の断面構造
|
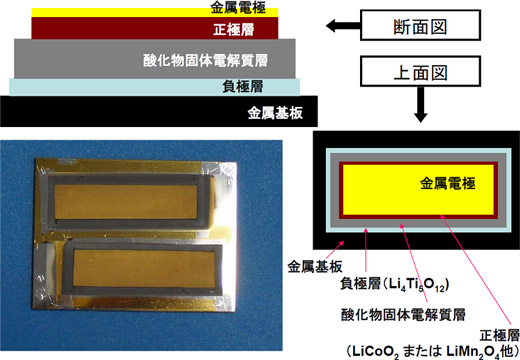 |
図4 今回試作した全固体型Liイオン電池
|
今回、試作した全固体型Liイオン電池はまだ初期段階で、その性能はまだ実用レベルに達していないが、常温プロセスであるAD法で作製した酸化物系全固体型薄膜Liイオン電池が動作したことは、AD法が蓄電池を実現する有力な作製法の1つであることを立証している。今後、より高性能な固体電解質材料を探索すると同時に、薄膜の微細構造を最適化することで、従来型のLiイオン電池を超える性能の実現を目指す。