独立行政法人 産業技術総合研究所【理事長 吉川 弘之】(以下「産総研」という)先進製造プロセス研究部門【部門長 三留 秀人】高温部材化プロセス研究グループ 研究グループ長、北英紀らは、株式会社クボタ【代表取締役社長 幡掛 大輔】(以下(株)クボタという)と共同で、低品位ケイ素原料を用いて高強度の窒化ケイ素を合成する技術を開発した。
今回開発した窒化ケイ素は、低純度で粗大なケイ素粉末と触媒機能を有する焼結助剤の混合粉末を、水と短時間で混合し、成形、窒化・焼結で作製できる特徴がある。実際に作られた窒化ケイ素サンプルは、短時間混合のため原料の粒径は粗いままにも関わらず、その状態で成形焼結しても、従来の微細な原料を使用した場合に匹敵する緻密な組織になり(図1参照)、また機械的特性も同レベルになることを確認した。今回開発した窒化ケイ素は、水を溶媒として作製できるため環境負荷が少なく、低品位の原料を使用できるため価格は従来の1/5~1/25程度になり、全体コストに占める原料コストの割合の大きい大型の部材への適用が期待される。
本技術の詳細は9月19日~21日にかけて山梨大学で開催される日本セラミックス協会秋季シンポジウムで発表される。
|
原料粉末性状(粗い、粒度分布広い) |
焼結後の組織(緻密で微細) |
(図1) |
世界的な規模で炭酸ガスの排出規制の動きがあり、燃費改善に有効な部品のアルミ化が進んでいる。エンジン等に適用されるアルミ部品は重力・低圧鋳造、ダイキャスト・プロセスにより製造されるが、製造プロセスの熱エネルギーロスの低減や鋳造部材の保守間隔の長期化を必要としている。特に、アルミ鋳造のプロセスでは、上記の課題を解決するために耐熱・耐食性に優れる窒化ケイ素セラミックスが保護管やラドル、ストーク、ヒータチューブ等の製造用部品として活用されつつある。しかし、特性が優れた窒化ケイ素セラミックスを作製するには、高価な原材料を使用する必要が有り、コスト高は大きな課題になっている。このため、低コストの材料を使っても優れた特性を示す窒化ケイ素セラミックスの実現が望まれていた。
産総研は(株)クボタと共同で、高価な窒化ケイ素粉末に比べて格段に安価(1/10~1/50程度、キログラム当たり数百円)な低品位なケイ素(Si)粉末を出発原料として、緻密で高強度の窒化ケイ素の開発を進めてきた。
ケイ素と焼結助剤を使って成形体を作製し窒化後、緻密化させる手法は古くから知られていたが、高強度の窒化ケイ素を得るためにはケイ素粉末を混合過程で微細化する必要があった。また、ケイ素は粉末状態になると活性になるため、混合溶媒としてアルコール等の有機系溶媒を使用せざるを得なかった。その結果、原料が安くても、プロセスで発生するコストが高く、環境負荷を大きくするなどの問題があり普及するに至っていない。
一方、ケイ素粉末が粗ければ不活性なので有機系溶媒も不要であるが、窒化が困難となり、長時間を要するためにプロセス全体でみると、結局、高コストとなってしまうといった課題があった。
コストの低減を目指すため、価格の安い低位品なケイ素を主原料とすることを前提として、まず添加する焼結助剤や焼結温度の影響について検討を行った。その結果、図2にみられるように、原材料が平均粒径で45µm、中には100µmの粗大な粒子を含む粉末であり、また高度な精製はなされず純度が99%以下といった低品位なケイ素粉末であっても、ジルコニアとスピネルを含む焼結助剤を添加した混合粉末では、容易に窒化が進む事を明らかにした。さらには図3のように、使用するジルコニアの種類によっても窒化速度が異なっていた。
ケイ素の窒化触媒としては、これまで酸化鉄が有効とされているが、酸化鉄の場合、窒化ケイ素と親和性が低く、焼結後に欠陥となり、強度低下をまねきやすい。一方、ジルコニアはケイ素の窒化に伴う発熱を制御する機能があり溶融を抑え窒化促進に効果がある上、窒化ケイ素と親和性が高く、焼結助剤としての効果を有すると考えている。
窒化のメカニズムについても解明を進め、その一例として1,750℃で焼結した試料の組織を図4に示す。また、機械的な強度に関しても、表1に示すように本材料では平均で700MPa以上の高強度を有する焼結体を得た。低品位なケイ素粉末を用い、粗大な粒子のまま使用しても、従来と遜色のないレベルの強度を得られることが判った。
|
図2 ケイ素原料粉末性状 |
図4 窒化ケイ素焼結体の組織 |
|
図3 イットリウム(Y)含有量の異なるジルコニア(ZrO2)添加が、ケイ素の窒化に及ぼす影響(窒素気流中1300℃で保持) |
表1 |
原料価格、及び焼結体強度の比較例 |
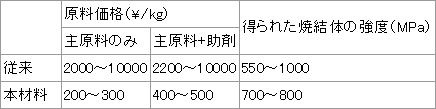 |
|
今回開発した材料を使って、アルミ鋳造用の部品を中心とする大型部品をターゲットとして部材化技術を確立し、実用化を図る。