独立行政法人 産業技術総合研究所【理事長 吉川 弘之】(以下「産総研」という)先進製造プロセス研究部門【部門長 神崎 修三】 集積加工研究グループ 明渡 純 研究グループ長、小木曽久人主任研究員は、サブマイクロメートル粒径(サブマイクロメートル:ここでは0.1マイクロメートル程度を示し1000万分の1メートル)の微粒子一個一個の形状の測定と、その微粒子の圧縮試験ができる微粒子強度測定装置を開発した。
直径が1マイクロメートル以下の微粒子は、ファインセラミックスやナノマテリアル材料の原料として、注目されている。しかし、このような小さな粒子の力学的強度(以下、単に強度と示す)測定を行う事は不可能であり、微粒子に圧力や衝撃が加わったとき、その粒子がどうなるかが予想できず、微粒子を応用する材料技術の発展が遅れていた。本装置は、この問題を解決するため、微粒子一個一個の強度測定を可能にしたものであり、実際にサブマイクロメートルサイズのアルミナ微粒子の強度測定に成功したものである。この技術により、微粒子の強度分布や、圧力によって生じる変形を調べる事が可能になり、粉体の基本的な特性を評価する技術として、セラミック技術や粉体を利用する医薬品や化粧品などの分野での利用が期待される。
本装置と微粒子の強度評価研究の詳細は、2005年12月10~11日に東京で開催されるMRS-J学術講演会において発表する予定である。
強度測定を行った実験結果
|
|
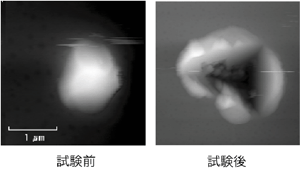
圧縮試験前後の微粒子の様子
|
最近、粒径が1マイクロメートル以下の微粒子を利用した技術が、電子セラミックスや医薬・化粧品などの分野で注目されている。しかし、微粒子の粒径分布を計測する技術については開発が進んでいたが、基本的な物性である強度に関しては、このように小さな粒子では、実際の計測は行われてこなかった。微粒子を利用した新技術開発においては、微粒子の基本物性の測定は重要な技術である。このような測定技術がなくては微粒子を使った製品の安定性がはかれず、微粒子を利用した技術の実用化の障害になるおそれがあり、測定技術の実現が待たれている。
産総研では、独自に開発したエアロゾルデポジション法を利用したセラミック材料の低温での表面改質技術(コーティング技術)の研究開発を行ってきている。この技術は、粒径が1マイクロメートル以下の微粒子をエアロゾル状態にして、基板表面に吹き付けただけでセラミックス膜を室温で形成する技術であり、世界的に注目されている。この成膜過程においては、微粒子が衝突によって破砕することが、重要な役割を持つ事がわかってきた。吹き付ける微粒子の強度が膜の性質に大きな影響を与えるので、微粒子強度を知る事が極めて重要になる。しかしながら、従来このような微粒子の強度測定を行える装置がなく、本研究開発を行うにいたった。
なお、本研究開発は、独立行政法人 新エネルギー・産業技術総合開発機構の委託事業「ナノレベル電子セラミックス低温成形・集積化技術プロジェクト(平成14~18年度)」による支援を受けている。また、本研究開発においては一部株式会社ナノテックの協力を受けた。
本装置(図1)の測定原理は、図2のように、微粒子をダイヤモンド基板とダイヤモンド圧子の間に挟み込んで圧縮試験を行うものである。原理自体は極めてシンプルなものであるが、サブマイクロメートルサイズの微粒子でこれを実現するためには、以下のような技術課題を克服しなければならなかった。
-
サブマイクロメートル粒子の検出とその粒径・形状測定
-
ダイヤモンド圧子先端の平坦部の加工
-
形状を観察した微粒子を間違いなく圧縮試験するためのサンプルステージの精度
従来の粒子を圧縮試験する装置では、光学顕微鏡を用いて観測しており光の波長の関係で1000倍程度の倍率が限界なので、サブマイクロメートルサイズの微粒子を正確に観測することはできなかった。粒子の強度測定には、粒子の大きさや形状を正確に知ることが不可欠であり、本装置では、光学顕微鏡に加えて、このような小さな微粒子の形状を測定するため特殊な探針を持つ原子間力顕微鏡(AFM)を備えた。これによりナノメートル(10億分の1メートル)の測定分解能を確保した。
微粒子の機械強度測定には図2のように微粒子を正しく挟み込む必要があり、ダイヤモンド圧子先端は平坦でなければならない。しかし、平坦部の大きさが粒子の大きさより大きいと、図3のように複数の粒子を圧縮したり、基板と接触しながら圧縮してしまい単一の粒子の圧縮試験が正しく実行されない。市販のダイヤモンド圧子では、平坦部が数10マイクロメートル以上なので、このままでは粒径が1マイクロメートル以下の微粒子に対しては使用できない。そこで、本装置では、図4のように集束イオンビーム(FIB)加工により、平坦部が1マイクロメートル程度のダイヤモンド圧子を作製し装備することで、確実に微粒子一個の圧縮を行う事が可能になった。また、この先端部で微粒子を正確な位置で圧縮するため、0.1マイクロメートル精度の位置制御ステージを備え付けた。図5はその圧縮試験前後のアルミナ微粒子を原子間力顕微鏡で観察したものである。図6は、このアルミナ微粒子の圧縮試験時の、荷重-変位曲線(圧縮力と変形の程度との関係)である。この曲線から粒子がある力で急激に変形(破壊)を起こしている事がわかる。このときの圧縮力と、粒子の大きさから、粒子の強度を測定できる。図7は、いくつかの粒径のアルミナ微粒子の平均強度を測定した結果である。アルミナ微粒子の強度がサイズの-0.5乗に比例しており、このような粒子強度のサイズ効果(強度が、粒子サイズに影響をうける効果の事)が初めて実測された。従来、大きな材料中の結晶粒の大きさがマイクロメートルより小さくなると、その材料の強度が大きくなる事は知られていたが、複雑な要因がからみあっているため、強くなるメカニズムはわかっていなかった。今回、微粒子1個だけの強度を測定できたため、微粒子自体が強くなっていることが確認できた。
本装置により、粉体全体の強度分布や、微粒子強度のサイズ効果などの測定が可能になる。更に、産業用途への応用としては微粒子の製造方法と強度の関係の解明、品質管理や微粒子強度のデータベース化などが期待される。
図2 微粒子圧縮試験の模式図
|
|
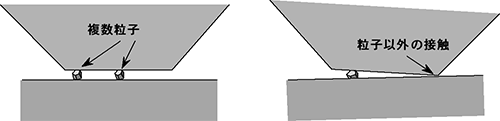
図3 粒子より大きな平坦部をもつ先端の問題
|
図4 ダイヤモンド圧子先端の集束イオンビームによる加工
|
|
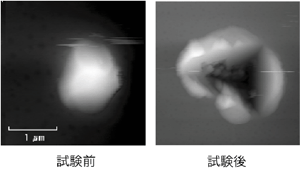
図5 圧縮試験前後の微粒子
|
図6 アルミナ微粒子の圧縮試験時の荷重と変位の関係
|
|
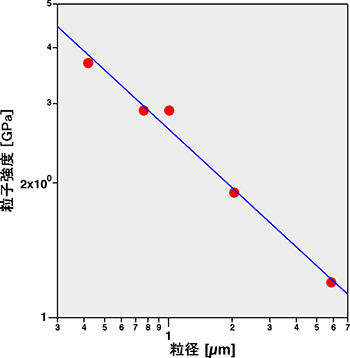
図7 実測したアルミナ微粒子の粒径と強度の関係
|
今後、この技術を用い、各種粉体の強度を測定し、粉体物性のデータベースを拡充し、粉体の製造方法と強度の関係、あるいは、粉体のサイズと強度や変形強度の関係など、粉体技術の基礎的な知見の拡充をはかり、産総研の独自技術である微粒子を使ったコーティング技術の産業レベルでの実用化を目指す。
また、現状では、粒径がおよそ0.1マイクロメートル(100ナノメートル)程度までの評価が限界であるが、10ナノメートル程度の微粒子の評価を目指していきたいと考えている。