独立行政法人 産業技術総合研究所【理事長 吉川 弘之】(以下「産総研」という)知能システム研究部門【部門長 谷江 和雄】の宮下 和雄 主任研究員は、株式会社日立東日本ソリューションズ【代表取締役社長 大多和 英行】(以下「日立TO」という)と共同で、半導体の製造コストを大幅に削減する生産制御手法を開発した。
産総研は、超高速な生産シミュレーション技術を開発し、半導体の製造コスト削減と生産変動に対する頑健さの鍵をにぎる工程内在庫の最適値をリアルタイムに求める手法の開発に成功した。日立TOは、分散型生産制御手法を開発し、生産設備の故障などの生産変動が起きても、各工程が自律的に生産を調整し常に最適在庫量を維持することを可能とした。
半導体などの大規模複雑な製造工程では、生産シミュレーションには長い時間がかかる上に、製造プロセスの不具合などが頻発するため、需要を満足する生産実施に必要な最適在庫量を臨機応変に設定するのは不可能であった。その結果、工程内の在庫に対する管理が困難になり、過剰な在庫を抱えることによる製造コストの増大を招いていた。
このような背景において、本手法では、まず、従来の生産シミュレーション手法よりも20~100倍以上も高速なシミュレーション技術に基づき、遺伝的アルゴリズム(GA)とクラスタコンピューティング技術を用いて、最適在庫量を20分以下で計算する。更に、分散型生産制御は、工程毎にリアルタイムに最適在庫を維持することにより、製造工程内の在庫を常に適切に管理することを可能にした。この生産制御手法によって、半導体製造工程内の在庫量を従来の半分以下に抑えられるため、半導体製造に係るコストが大幅に削減され、国内半導体産業の国際競争力を格段に高めることができると期待される。
今後、本生産制御手法を半導体製造実施システム(MES)に組み込んで、実際の半導体製造工程に適用する予定である。さらに、半導体以外では、液晶・プラズマディスプレイなどのハイテクデバイス部品の製造工程にも応用する予定である。
なお本手法の詳細は、2003年12月7~10日に米国ニューオリンズで開催される2003 Winter Simulation Conference(WSC '03)で発表されるほか、2003年11月13日に茨城県つくば市で開催される産総研 知能システム研究部門 研究成果展示会-オープンハウス2003-でも展示される。また本研究に関する特許を現在数件出願中である。
国内半導体産業では、産学官一体になっての活発な製品・プロセスの研究開発により、新たな市場獲得努力がなされている。その一方、システムLSIに代表される最先端プロセスを用いた新製品の多品種変量生産化の進展に伴って、国内半導体産業の復権には、製造・生産技術部門の再生・強化が不可欠であるという指摘がされている。しかしながら、半導体産業には、長い生産リードタイム(2ヶ月程度)、短い製品ライフサイクル(6ヶ月以下)、常に更新され安定しない生産プロセスなどの困難な問題があり、従来、日本の製造業が得意としてきたジャストインタイム生産方式などの生産手法の適用が困難である。反面、新興産業国は、安価な労働力や生産資材を利して半導体生産でも高いコスト競争力を持ち、その国際競争力を急速に増している。そこで、国内半導体産業の製造力を強化するため、本研究では上記半導体産業の特質を踏まえた大規模ロバストな(耐故障性の高い)生産制御手法の開発を行った。【図1参照】
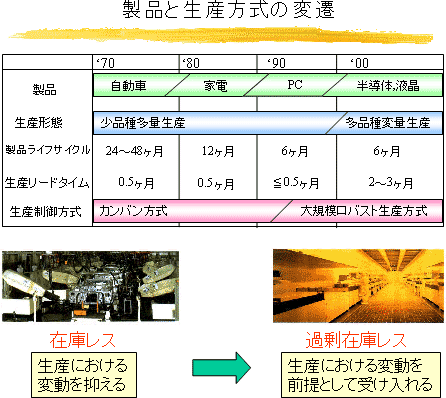
|
図1 本研究の背景
|
産総研知能システム研究部門分散システムデザイングループでは、シミュレーション技術、人工知能技術などを核にして、半導体製造工程や巨大テーマパークなど、大規模複雑なシステムの自律分散的な制御手法の研究開発を進めている。また、日立TOは生産計画システムや生産制御システムなどの製品の開発販売を行っている。かねてより両者は、スケジューリング学会などの場において、アカデミズム・実務家の立場から国内半導体産業の製造力強化のための生産制御方式に関する議論を重ねてきた。本研究は、産総研で実施中の両者の共同研究「大規模ロバスト生産方式下における分散スケジューリング方式に関する研究」から生まれた研究成果である。
(1)超高速な生産シミュレータ(CONSTIN)の開発
【図2】は、本研究で開発した超高速な生産シミュレータ(CONSTIN)でPeriodを一定周期としてシミュレーションを行った場合のある工程における時間による在庫量(WIP)の変化の様子を青線で示し、伝統的な事象ベースシミュレータによる在庫量の変化の様子を赤線で示している。従来の事象ベース方式の生産シミュレーションでは、工場内で発生する全ての事象(全ての機械における生産開始、終了、故障など)に関して、赤線で示すように逐一、次の状態推移を細かく計算するため、莫大な計算時間が必要とされる。そこで、本研究で開発した超高速な生産シミュレータ(CONSTIN)では、一定周期ごとにのみ、その周期内で生じた全ての事象(加工開始、加工終了、機械故障など)による変化をまとめて製造工程の状態推移を計算することにより、計算量の大幅な削減を行った。
CONSTINでは、一周期内での事象の発生をまとめるため、【図2】で示すように全ての生産工程間の在庫移動は各Period終了時点での生産量から決定するものとし、在庫移動はPeriodごとにのみしか行わないとする。その結果、CONSTINでは、工程内在庫量の時間推移は【図2】の青線で示すように周期内で一定となる。したがって、在庫量は前周期に蓄積された在庫と今周期内の生産実施量から決定できるので、周期単位のシミュレーションで計算することができるようになる。したがって、周期(Period)の値を大きく設定する事で長時間にわたるシミュレーション結果も高速で計算できる。
また、周期が長くなるほど、周期内に蓄積される工程内在庫量が大きくなり、計算誤差も大きくなると考えられるが、実際の生産工程における平均的なロット生産時間を周期とすることにより、そうした問題は適切に解決することができる。
したがって、上の周期を適切に設定することにより、CONSTINは、全ての事象による工程の変化の様子を逐次的にシミュレーションする従来の事象ベースシミュレータに比べて、シミュレーション精度を同等レベルに保ちながら、20倍から100倍程度高速なシミュレーションを行うことができる。
(2)クラスタコンピュータを用いてGAによる高速な最適化を実現
遺伝的アルゴリズム(GA)の計算において、最も計算時間のかかる各遺伝子の適応度の計算に関して、遺伝子集団を分割しクラスタコンピュータに均等に分散させることにより、並列計算を行う。これにより、大規模半導体製造工程の最適在庫量の計算に際しては、CPU台数にほぼ比例した計算速度の向上が実現された。
(3)高速シミュレーションと分散型生産制御の統合による柔軟でロバストな生産実施
分散型生産制御では、生産を実施する設備毎にローカルに生産をコントロールする。中央のサーバによる集中的な生産制御方式に比べ、耐故障性に優れ、突発的な事象に対する即応性の点でも有利であると言われる。しかし、全体的に最適な制御を終始一貫して行うためには、各設備に対する適切な目標設定と、設備間での高度な協調処理が必須である。従来の分散生産制御では、各生産設備において固有の生産規則(次に何をどれだけ生産するか)を設定することにより、柔軟でロバストな制御が実現できるとされていた。しかしながら、実際には各設備の生産規則が複雑に相互作用を行って最終製品が完成されるため、各設備においてどのような生産規則が適切かを決定することは困難であり、ほとんどの場合には、そうした機能を十分に活用できなかった。本研究では、【図3】に示すように、各生産設備に対して、適切な目標在庫量が上位のCONSTINによって指示されるため、各生産設備の生産規則は、指示された目標在庫量を維持することに専念すれば良いことになる。生産設備の特質に応じて、目標在庫を維持するために適切な生産規則を設定することは比較的容易に行えるので、本手法により分散制御における柔軟性・ロバスト性と、全体最適性を兼ね備えた生産実施が実現できる。【図4】は、CONSTINによって指示された目標在庫を維持して生産を行った結果(上グラフは生産レートの時間推移、下グラフは納期遅れ量の時間推移を示す)である。この【図4】は時間100付近で設備故障のため生産レートが落ち、納期遅れとなる製品が増えても、適正在庫を保持しているために、すぐに生産レートは定常状態に復旧し、納期遅れの製品も挽回されている様子を示している。
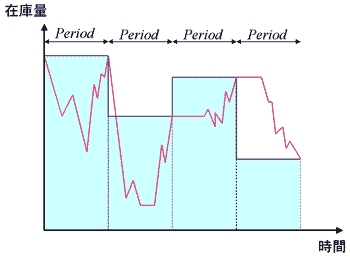
|
図2 事象ベースシミュレータによる在庫量の変化(赤線)と
超高速な生産シミュレータ(CONSTIN)による在庫量の変化(青線)
|
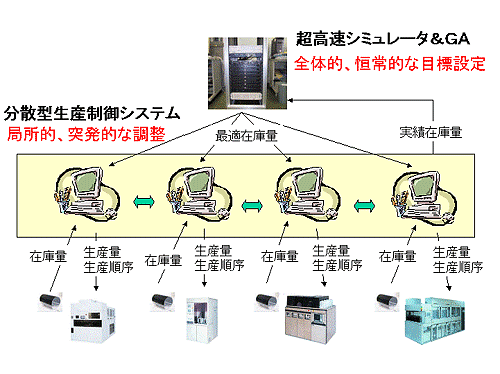 |
図3 本研究の構成
|
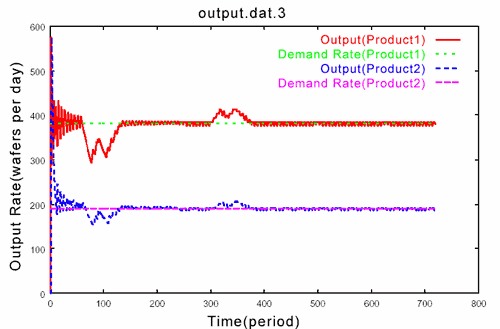
|
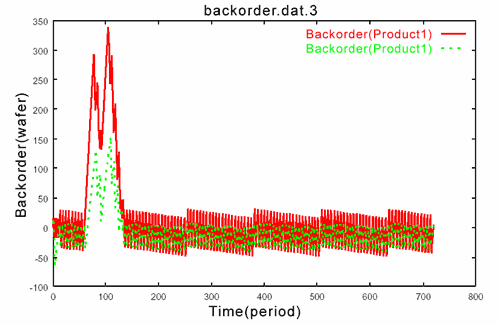 |
図4 最適在庫の下での生産レートと納期遅れ量の推移
|
今後は本生産制御手法を半導体の製造実施システム(MES)へ組み込んで、分散型生産制御手法の有効性を検証し、実用化につなげていく予定である。